Nowadays plastic goods' application fully our life,whatever in household or industrial. But do you really know how to make a plastic product? Keep reading, this article will tell you.
Injection molding usually defined as a thermoplastic polymer is heated above its melting point, resulting in the conversion of the solid polymer to a molten fluid with a reasonably low viscosity. This melt is mechanically forced, that is, injected, into a mold in the shape of the desired final object. For industry production, injection molding is one of the most important processes for mass-production of objects from thermoplastics. Workers usually pour dry plastic raw materials (such as:ABDS,PP,TPU,PA66) into the barrel of the injection molding machine. Then according to different product requirements, different temperatures and injection speeds are designed. Then set different temperatures and injection speeds according to different product requirements. After final cooling to form the product, it is ejected by the ejector pin.
1.Product privacy and security
During the product release process, it often happens that products that have been designed for a long time have been pirated before they are released. This is often due to the fact that customers use various ready-made molds to splice them together during the design and injection molding process, and do not have their own set of molds. When you customize a set of exclusive molds for your products, this problem will no longer occur, because we will keep the molds on the principle that only you can use them, and perform regular maintenance on them for your benefit. Use it anytime later.
2.Complexity
When you choose to customize a set of molds, your products will no longer be limited by structure and molds. Due to the high degree of freedom in customization, you can design complex product structures according to your needs instead of splicing them together from multiple molds. This will greatly improve the integrity and integrity of the product. With the current wide range of applications of injection molds and 3D drawings, the products you design can range from household to industrial products.
3.Lower cost
From a production point of view, customizing a mold may require a higher cost than using a ready-made mold. However, from a production point of view, injection molding is a mass production process and long-term use of ready-made molds for splicing production. The subsequent costs are very high, so when you choose a customized mold, you will not need to pay anything for the mold.
Design the Mold in CAD
The design of the mold is one of the most important steps in the process. This is the step where you have to decide what the part will look like, how it will be made and what features it will have. Injection molding is a complex process, and the mold is a major part of that. The mold needs to be able to withstand the high pressure and heat of the injection process, as well as the repeated use. That’s why it’s important to get the design of the mold right the first time. CAD software can help you create a perfect 3D model of your part that you can use to create the mold.
3D Print the Mold
The final step is to print the mold using a 3D printer. This will create the final, actual-sized mold. If you’re not sure how to go about this, there are plenty of online tutorials to help you out. You can also find 3D printing services that will do the job for you. Printing the mold is a crucial step, as it will ensure the finished product is of the highest quality.
If you want to know more about design mold, you can read Mold Design and Manufacturing for Plastic Components
1.slider
When the slider is combined by splicing, it cannot completely fit the mold. When the mold is opened and closed, it is easy to cause the inclined top to break.
2.water channel
There is no water flow channel planned when designing the mold, which is prone to problems with product cooling. Moreover, after long-term use of the mold, the temperature of the mold will become higher and higher, eventually leading to deformation of the product or deviation of the hole position.
3.Mold wear
During the design process of the mold, because no slots were added to allow oil to lubricate the mold, the friction coefficient between the iron blocks during the grinding process was too large, causing damage to the mold.
China injection mold companyNowadays plastic goods' application fully our life,whatever in household or industrial. But do you really know how to make a plastic product? Keep reading, this article will tell you.
Injection molding usually defined as a thermoplastic polymer is heated above its melting point, resulting in the conversion of the solid polymer to a molten fluid with a reasonably low viscosity. This melt is mechanically forced, that is, injected, into a mold in the shape of the desired final object. For industry production, injection molding is one of the most important processes for mass-production of objects from thermoplastics. Workers usually pour dry plastic raw materials (such as:ABDS,PP,TPU,PA66) into the barrel of the injection molding machine. Then according to different product requirements, different temperatures and injection speeds are designed. Then set different temperatures and injection speeds according to different product requirements. After final cooling to form the product, it is ejected by the ejector pin.
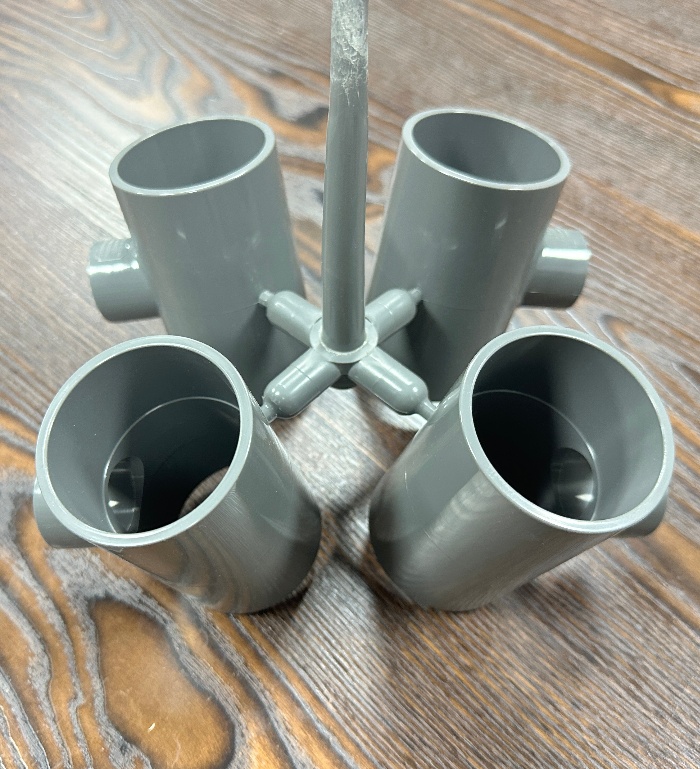
1.Product privacy and security
During the product release process, it often happens that products that have been designed for a long time have been pirated before they are released. This is often due to the fact that customers use various ready-made molds to splice them together during the design and injection molding process, and do not have their own set of molds. When you customize a set of exclusive molds for your products, this problem will no longer occur, because we will keep the molds on the principle that only you can use them, and perform regular maintenance on them for your benefit. Use it anytime later.
2.Complexity
When you choose to customize a set of molds, your products will no longer be limited by structure and molds. Due to the high degree of freedom in customization, you can design complex product structures according to your needs instead of splicing them together from multiple molds. This will greatly improve the integrity and integrity of the product. With the current wide range of applications of injection molds and 3D drawings, the products you design can range from household to industrial products.
3.Lower cost
From a production point of view, customizing a mold may require a higher cost than using a ready-made mold. However, from a production point of view, injection molding is a mass production process and long-term use of ready-made molds for splicing production. The subsequent costs are very high, so when you choose a customized mold, you will not need to pay anything for the mold.
Design the Mold in CAD
The design of the mold is one of the most important steps in the process. This is the step where you have to decide what the part will look like, how it will be made and what features it will have. Injection molding is a complex process, and the mold is a major part of that. The mold needs to be able to withstand the high pressure and heat of the injection process, as well as the repeated use. That’s why it’s important to get the design of the mold right the first time. CAD software can help you create a perfect 3D model of your part that you can use to create the mold.
3D Print the Mold
The final step is to print the mold using a 3D printer. This will create the final, actual-sized mold. If you’re not sure how to go about this, there are plenty of online tutorials to help you out. You can also find 3D printing services that will do the job for you. Printing the mold is a crucial step, as it will ensure the finished product is of the highest quality.
If you want to know more about design mold, you can read Mold Design and Manufacturing for Plastic Components
1.slider
When the slider is combined by splicing, it cannot completely fit the mold. When the mold is opened and closed, it is easy to cause the inclined top to break.
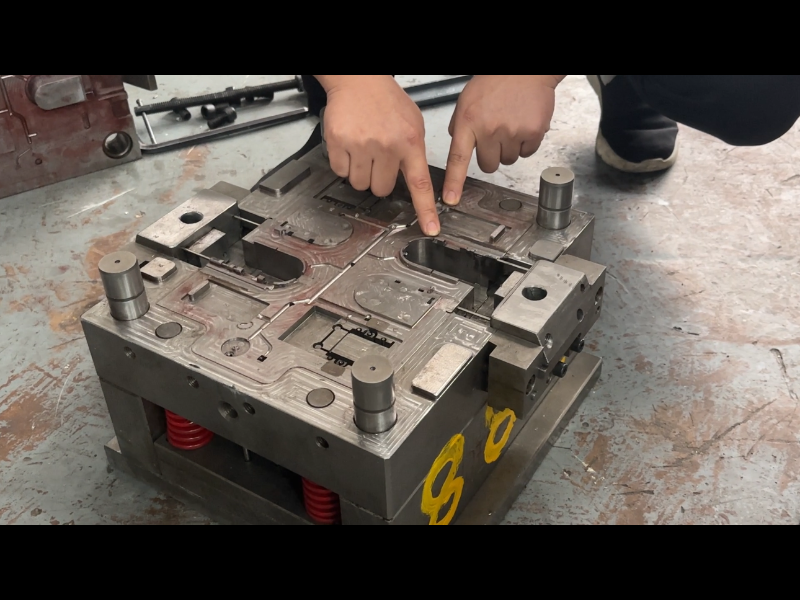
2.water channel
There is no water flow channel planned when designing the mold, which is prone to problems with product cooling. Moreover, after long-term use of the mold, the temperature of the mold will become higher and higher, eventually leading to deformation of the product or deviation of the hole position.
3.Mold wear
During the design process of the mold, because no slots were added to allow oil to lubricate the mold, the friction coefficient between the iron blocks during the grinding process was too large, causing damage to the mold.
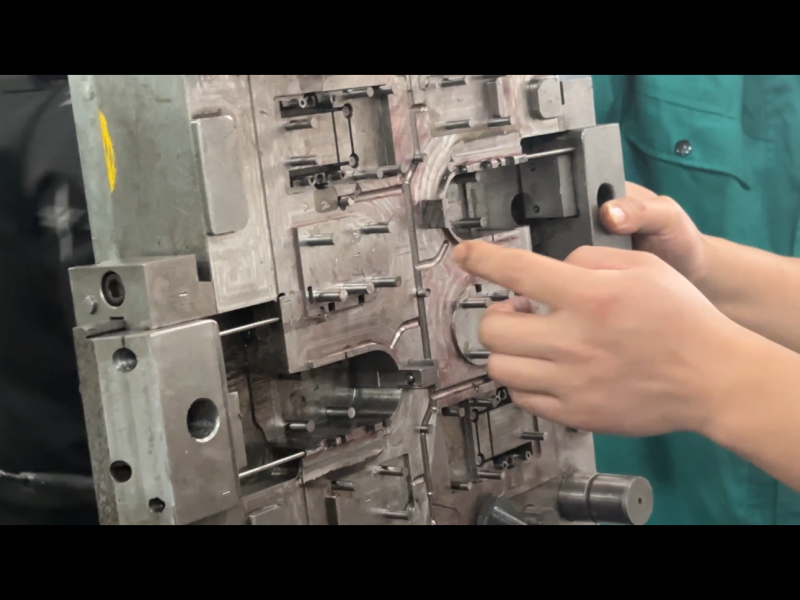
4.Product slot allocation is unreasonable
Since injection molding involves injecting high-temperature molten liquid clinker into the groove of the mold for final cooling of the product, the mold cavity of large products needs to be closer to the glue inlet to prevent the temperature from cooling due to the long distance and the to inability successfully inject into the mold. But the molds for small products require less plastic, so the grooves are usually designed at the edge of the mold.
5.The metal of remain in the original mold
The metal of remain in the original mold aren’t replaced by inserts. If damage occurs later, the entire remaining part of the original body needs to be wire-cut and then re-inserted.
If you would like to know any more related information about injection molding process or mold making, please feel free to contact our professional team.
article source: https://www.chinaruicheng.com/news/china-injection-mold-company/
Media Contact
Company Name: Xiamen Ruicheng Industrial Design Co., Ltd.
Email: Send Email
Country: China
Website: https://www.chinaruicheng.com/